
Dynamic milling brings the required technologies together, making it simple to create roughing programs that use advanced cutting tools. The focal point for applying constant chip load roughing in a shop is the CAD/CAM software. Once this low hurdle has been cleared, it is faster and easier to use this approach to roughing. Getting up to speed requires spending a little time learning how they work and how to use them correctly. These technologies are available, and most shops have at least some machines or cells where they can make use of constant chip load roughing strategies.

Reasonably rigid CNC machine tools with repeatable feeds and speeds (not necessarily high speed).During the last 50 years or so, technology developments have finally caught up with the theory to make the theoretical advantages of RCT practical for shops of any size.įour primary technologies determine how efficiently material can be removed during roughing operations. Unfortunately, users have no practical way to take advantage of this theoretical knowledge until recently. So not only is it possible to reduce tool wear and increase material removal at the same time, it is required if you are going to take full advantage of RCT. As stepovers are decreased, material removal rates must be increased to maintain constant chip loads and manage heat removal so that the cutting tool does not fail prematurely. As stepovers decrease, tool wear decreases, too, as long as the chip load remains constant. RCT has to do with the behavior of cutting tools when stepovers are 50 percent or less. Question: Is it possible to improve material removal efficiency and increase cutting tool life at the same time?Īnswer: It is not only possible, it is required.įor more than 50 years, material scientists have known that the theoretical answer to this question is “yes.” This understanding is based on a phenomenon known as radial chip thinning (RTC).
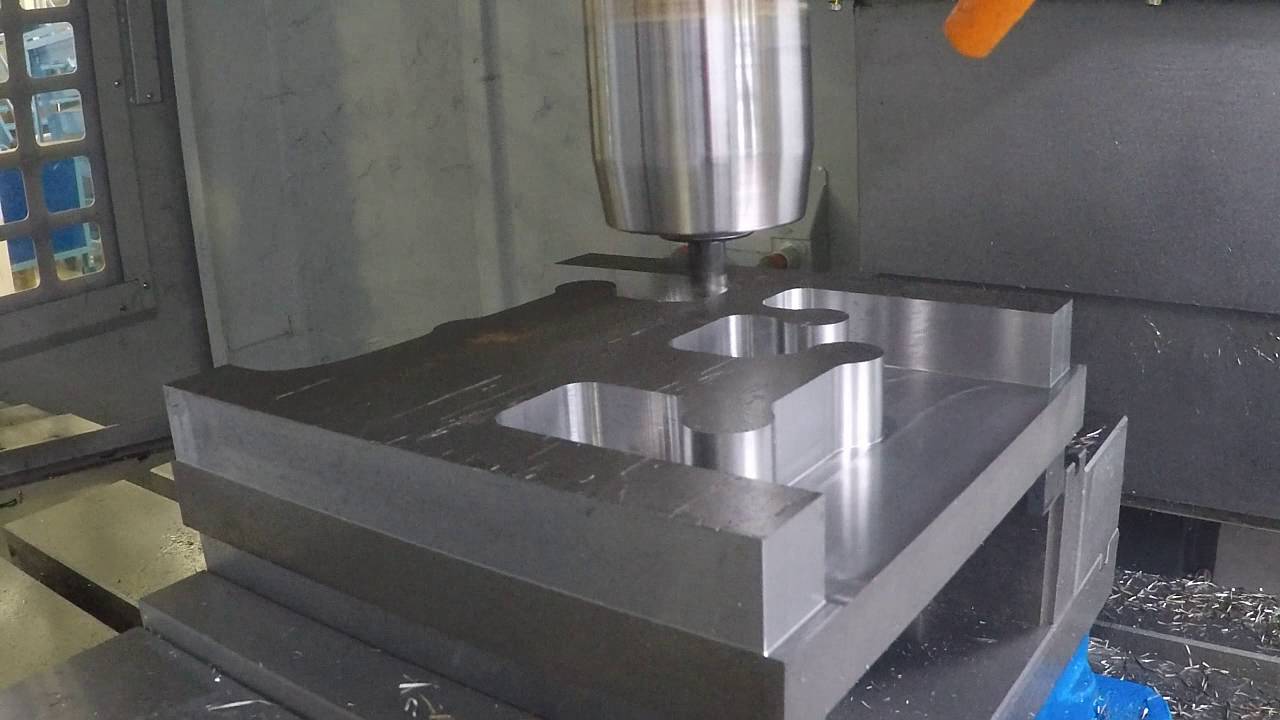
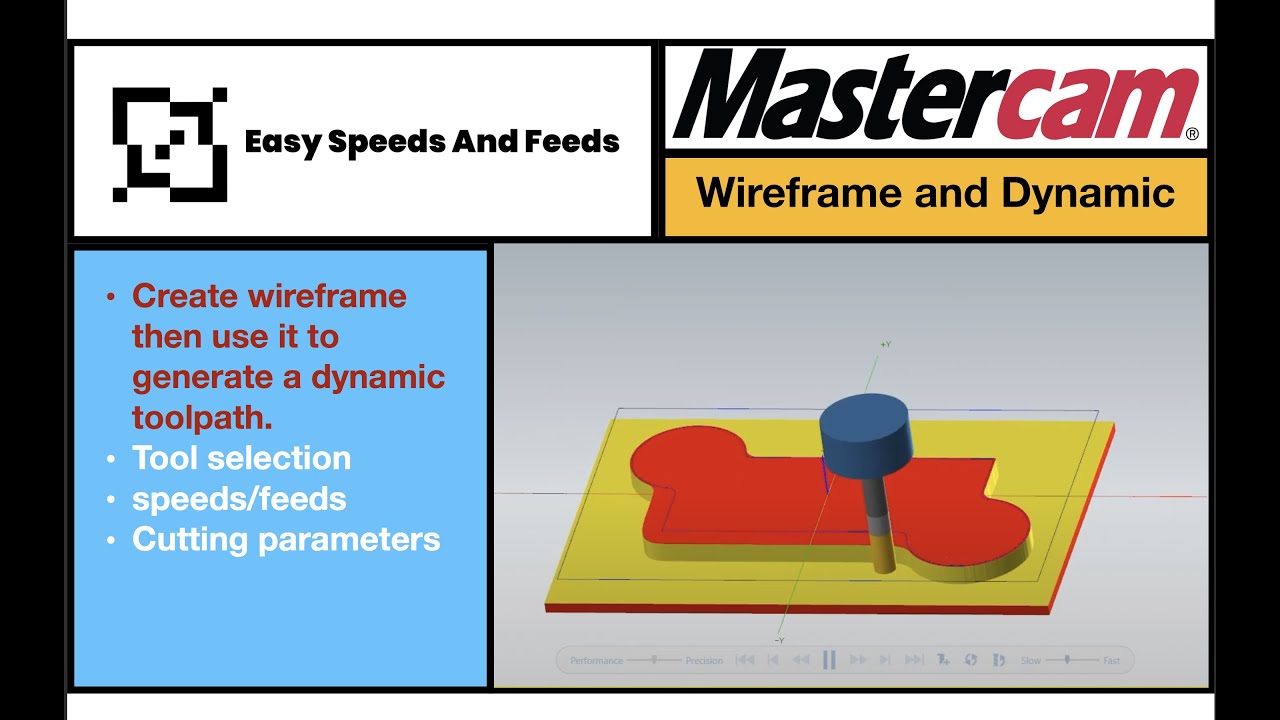
Here a small number of efficient, material-aware dynamic toolpaths are used to automatically blend transitions between steep and shallow areas to achieve the part geometry.
